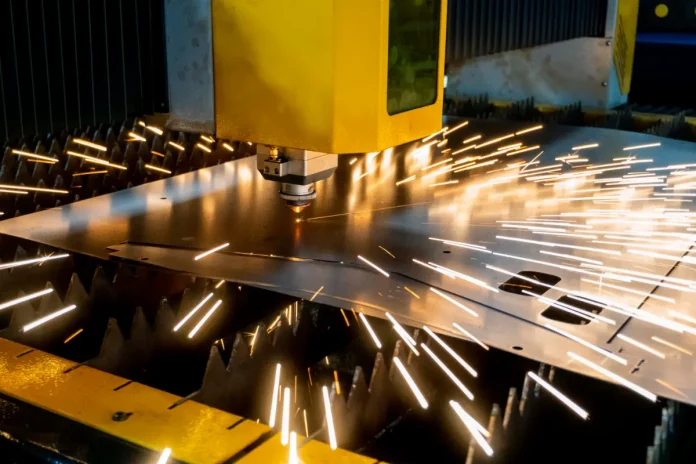
Cutting technology plays a vital role in manufacturing operations, shaping how products are made and ensuring precision in every cut.
From traditional methods like sawing and drilling to advanced ones like laser and waterjet cutting, the right technology can boost efficiency and quality.
This guide will explore new cutting technologies that are revolutionizing manufacturing.
Types of Cutting Technologies
There are several cutting technologies commonly used in manufacturing operations. Each has its own advantages, depending on the material being processed and the level of precision required.
Traditional Cutting Methods
Manufacturers have used traditional cutting methods for decades. These include sawing, drilling, and milling. These methods are effective for simple tasks but may lack the precision needed for complex projects. They often involve manual handling and are time-consuming compared to modern cutting techniques.
Laser Cutting Technology
Laser cutting is a powerful tool used in many manufacturing operations. But what does laser cutting do? It uses a high-energy laser beam to precisely cut or engrave materials like:
- metal
- plastic
- wood
This method is very accurate and efficient. It lets manufacturers create intricate designs with minimal waste. Laser cutting is ideal for industries where precision is critical. These include automotive, aerospace, and electronics.
Waterjet Cutting
Waterjet cutting is another advanced tech. It uses high-pressure water mixed with abrasives to cut metal, stone, and glass.
This method is beneficial for materials sensitive to high temperatures, as it doesn’t generate heat like laser cutting. Waterjet cutting provides a smooth finish and is versatile for various manufacturing operations.
Plasma Cutting
Plasma cutting uses an accelerated jet of hot plasma to cut through conductive materials such as:
- steel
- aluminum
- copper
It is known for its speed and ability to cut through thick materials. Plasma cutting is widely used in the construction and metal fabrication industries.
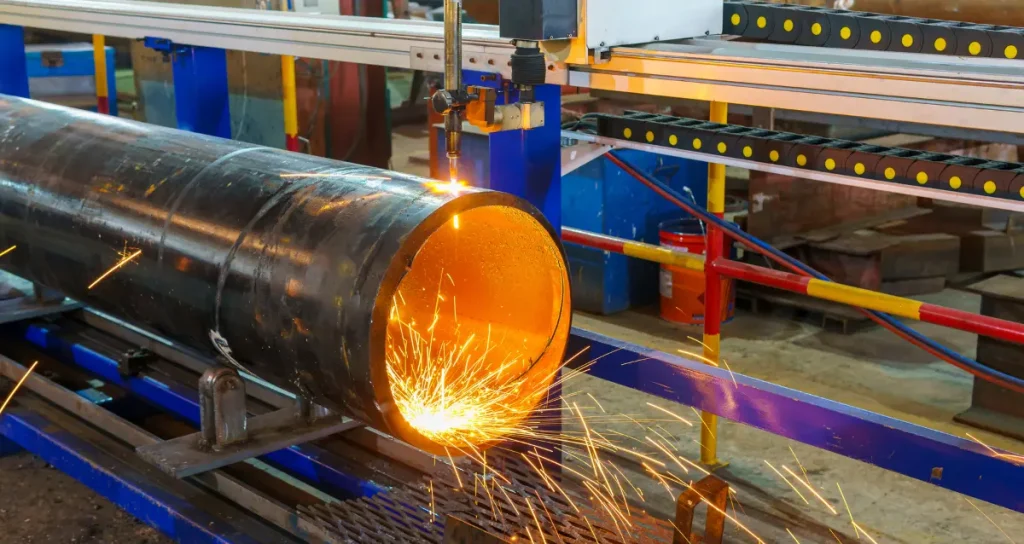
Benefits of Advanced Cutting Technologies
Modern cutting technologies improve manufacturing. They boost efficiency and quality.
Improved Precision and Accuracy
Advanced cutting technologies, like laser and waterjet cutting, offer unparalleled precision machining and accuracy. This ensures that all components meet exact specs. It reduces rework and improves the final product’s quality.
Increased Efficiency and Productivity
Modern cutting technologies can significantly speed up manufacturing operations. Automated processes allow faster production rates, reducing lead times and increasing productivity. This means manufacturers can meet tight deadlines without compromising quality.
Versatility in Material Usage
Advanced cutting methods can handle a wide range of materials, from metals and plastics to composites and ceramics. This lets manufacturers diversify their products and take on complex projects.
Cost-Effectiveness
Advanced cutting equipment has a high initial cost. But, it saves a lot long-term. Lower material waste, fewer errors, and faster production cut costs. So, it is a cost-effective choice for many manufacturers.
Enhancing Manufacturing Operations with Cutting Technology
Cutting technology is crucial for modern manufacturing operations. They offer precision machining, efficiency, and versatility. Using laser, waterjet, or plasma cutting, the right technology transforms product creation.
Understanding each method’s benefits helps manufacturers optimize operations and stay competitive. As technology advances, adopting cutting-edge solutions is key to maintaining excellence in manufacturing.
Looking for more? We’ve got plenty in store. Click here to keep the good times rolling!
FURTHER READING